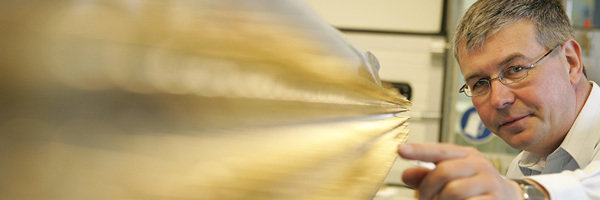
“What I find most fascinating is the variety of my work. We are always on the look out for new technologies and new materials, and have to come up with unconventional ideas for putting them into practice.”
How long have you been working at the Max Planck Institute for Physics and in what capacity?
Haubold: I have been working here since 2000, initially as a design engineer, then as head of the design group and, finally, as head of the mechanics department. The department currently has 30 employees. Three engineers, five technicians and a draughtswoman work in the design group. The equipment engineering group has a further 20 employees. I am no longer very involved in project work in my position and focus mainly on the technical and organisational management of the department.
What is your career background?
Haubold: Having completed an apprenticeship as a precision and general mechanic in the field of optical and scientific equipment engineering, I completed a degree in engineering via the “second-chance” education route. I did not want to be limited to producing mechanical parts and devices on the basis of other people’s designs. I wanted to develop scientific equipment based on my own ideas. For this reason, I also studied precision engineering/design in the evenings after work.1 After spending a few interesting years working in research, I then spent several successful years in the industry and eventually returned to my old “home” in basic research. Anyone with strength and determination can advance their career through second-chance education. This was definitely the right option for me.
Why does the Institute have a relatively large mechanics department? What do you and your colleagues have to do?
Haubold: The equipment needed by our scientists is not commercially available – this is where our skills come into play, in the creation of individual pieces. The design and production of the intricate measurement apparatus used by the scientists involves complex interaction between the designer, mechanic and scientist. The feasibility of complex designs is generally tested using models – we sometimes subject them to performance tests on the field in front of the Institute. If particular components need to be produced in large numbers, we only design a prototype in our department and outsource the production.
Complex projects of this nature usually take several years to carry out. How many projects are you and your employees working on at the moment and what are the biggest challenges involved?
Haubold: We are currently working on four projects. What is fascinating about them is that some of the parts we produce require us to work with tonnes of steel, while other parts are so tiny that they require precision engineering on the micrometer scale. We are unable to manufacture some things ourselves – in this case, we have to rely on outside specialists. In addition to this, we are always on the look-out for new materials which have low radiation levels, for example, or are very resistant to low temperatures, so that we can meet the special requirements of the scientific experiments carried out at the Institute. At the moment we are working with a special kind of copper that has to be stored underground and can only be delivered to the Institute shortly before it is used. The assembly of the equipment designed and manufactured by us is carried out on the experiment sites by our technicians, mainly in locations abroad.
Do you also provide training in your department?
Haubold: Yes, we have been involved in training since 2000 and have been very successful in this area – several of our trainees have completed their qualifications with distinction. The nomination of a former trainee for the MPS Azubi-Preis (trainee award) is further proof of the high quality of the training we provide. We select our trainees carefully from up to 200 applicants, and they also undergo aptitude testing. But the effort is worthwhile. Each time we can offer a trainee permanent employment in the department I am delighted, as this means that we can maintain a high level of skill and expertise in our department into the future.
Thank you very much Mr Haubold!
Thomas Haubold was interviewed by Barbara Abrell and Christina Beck